My Blog
Foam Cutter
Next up on the Low Temperature Differential Stirling Engine was the displacer block, which was made of foam. Before I could cut the foam, however, I needed a foam cutter! I found plans from Make Magazine in the Five-Minute Foam Factory article and adapted them to build my own specialty foam cutter.
In this project I reused a variable DC transformer (AKA speed controller) from an old train set, but you can find one here.
First, I measured out the distances I would need to cut, estimated some tolerances, and layed out the arm on some scrap plywood (everything here was a little loose).
…
Low Temperature Differential Stirling Engine: The Piston Assembly
The piston is an important part of the Stirling engine. It helps regulate the chamber pressure while simultaneously pulling the flywheel, causing the flywheel to rotate.
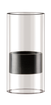
The piston needs to slide up and down quickly inside a tube, which makes fit essential. Since this was my first engine, I decided to purchase a graphite piston inside a glass tube online from Airpot.
I took one of the brass bolts that I was using to attach the block to the plates and filed it down on one side. I drilled through the flat part of the bolt so I could insert a wire hook to attach the piston to the flywheel later on.…
Low Temperature Differential Stirling Engine: Making the Displacer Chamber Ring
Between the two plates sits the displacer ring, made of clear acrylic plastic. The displacer ring forms the walls of the displacer chamber, within which air is heated and cooled and the displacer block moves.
To make the ring, I started with a long tube of acrylic from which I chopped a ring on the mitre saw. Next, using a mitre, I cut a circle of wood with a rough outer diameter, nearly the same size as the inner diameter of the tube. This will eventually act as an arbor on which I attach the ring to the lathe head:
…