With the Foam Cutter completed, now onto the displacer block (primarily made of foam)!
First, I cut a square chunk of foam out of a larger piece. Then I cut a circle of the foam using a nail set into wood. I stuck the foam on the nail and spun it around that point to make the circle.
Then I planed the cylinder into thinner disks using my horizontal foam cutter.
Next using a compass, I marked the circles which would hold the insert air filter material. I cut out those circles using a sharpened/cut-off steel tube. I also cut air-filter circles using the same tube.
I dabbed a ring of glue onto the inside of each circle and pushed the air filter disks into the holes.
Then, I made a solid brass piece to insert into the foam to connect to the flywheel.
Using an old soldering iron, I melted a circle into the foam to act as a well for the epoxy. (pictured: practicing)
I sunk the brass into the foam and filled the holes with epoxy. I put the foam on top of wax paper so that the bottom of the foam could fill in without sticking to my work-surface. I also put some level scrap pieces on top with the displacer bushing to make sure the brass dried evenly.
The displacer block was finished!
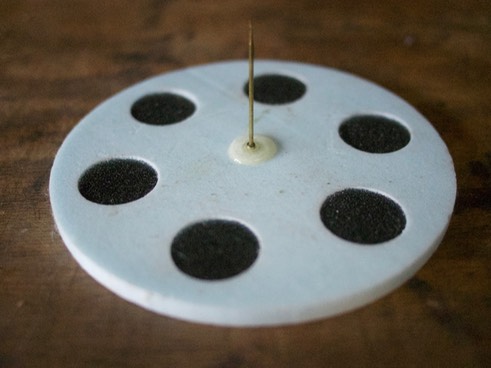